In the vapor compression refrigeration cycle, compressors play a vital role in pressurizing vaporized refrigerant from a low pressure and temperature to high pressure and temperature in preparation for traveling through a condenser. While compressors all serve the same primary function within an industrial refrigeration system, there are actually numerous types of compressors with varying methods of creating pressure. In the following sections, we will go over the various types of compressors, as well as their primary advantages and disadvantages.
Centrifugal
Centrifugal compressors, also known as turbo or radial compressors, pressurize a refrigerant by forcing the refrigerant through a rotating impeller. The impeller spins the refrigerant at an increasing speed, generating kinetic energy. The generated kinetic energy is then used to pressurize the refrigerant by passing it through a diffuser, which slows the vapor’s radial movement speed. This process of slowing the radial movement of the refrigerant converts the kinetic energy to potential energy in the form of pressure.
Centrifugal compressors have the largest capacity and are well suited for compressing large volumes of refrigerant. Additionally, centrifugal compressors can be set up in either single, two-stage, or multi-stage configurations to further compress the refrigerant to a higher pressure and temperature based on the application requirements.
Rotary-Vane
Rotary Vane compressors utilize a rotating drive shaft positioned eccentrically within a cylindrical housing that contains fixed inlet and discharge ports. Affixed to the drive shaft are adjustable vanes. As the drive shaft rotates, the vanes slide in and out to maintain contact with the interior walls of the compressor housing, resulting in the formation of chambers with varying sizes. Air then enters the largest of these chambers from the inlet port and is compressed as the drive shaft continues to rotate and the chamber size shrinks. Once the chamber reaches its smallest volume, the compressed air exits the compressor housing through the discharge port.
Rotary vane compressors have compact dimensions and operate efficiently, making them a preferred choice for low capacity applications, such as a household refrigerator or residential air conditioning unit. However, rotary compressors are also often used in the food and beverage industry for product handling applications.
Rotary-Screw
Rotary screw compressors contain two meshed male and female rotors that rotate together in opposite directions. The refrigerant enters the compressor through a suction port and gets trapped between the two rotating rotors. As the air travels through the rotors, the volume of space between the rotors decreases, compressing the refrigerant.
Screw compressors do not have any valves and do not use mechanical force, which allows the compressors to operate at high speed with large flow rates and a small footprint, while also reducing vibration.
Rotary-Scroll
Rotary scroll compressors contain two intermeshing spirals or scrolls with one spiral being fixed while the second orbits within it. As the spiral rotates, vapor pockets are formed. The pockets suck the refrigerant in and moves the vapor towards the center of the spiral. As the vapor gets closer to the center, the pockets continuously decrease in size, compressing the refrigeration.
Rotary scroll compressors have a small capacity of under 20 tons; however, they are highly efficient due to the absence of pistons, which allows them to reach 100% volumetric efficiency. Additionally, scroll compressors have low noise levels and maintenance requirements due to fewer moving parts.
Reciprocating
Reciprocating compressors have a design similar to a combustion engine and can contain anywhere from two to six pistons housed in individual cylinders. Each of these pistons are driven by a central crankshaft. As the pistons move downward, the refrigerant is sucked into the cylinder through an inlet valve. When the piston moves back upwards, the inlet valve closes, and the volume of space in the cylinder decreases, compressing the refrigerant. Once the refrigerant is sufficiently compressed, the necessary amount of force to open a discharge valve is achieved, and the refrigerant is expelled, allowing the cycle to repeat.
Reciprocating compressors are highly scalable, allowing them to be designed to a small capacity or a high capacity of hundreds of tons. The main detractors to reciprocating compressors are that they are very loud, have a high amount of vibration, and are inefficient.
About Process Solutions
Located near Seattle, Washington, Process Solutions has over 30 years of experience providing high-quality control systems. With over 100 engineers and technicians on staff and an output of over 3,000 industrial control panels per year, Process Solutions is the Northwest’s largest control systems integrator. In addition to custom motor control panels, Process Solutions’ control systems services include PLC and HMI programming, robot system integration, energy management, and industrial refrigeration control systems, SCADA integration, and DAQuery machine monitoring software.
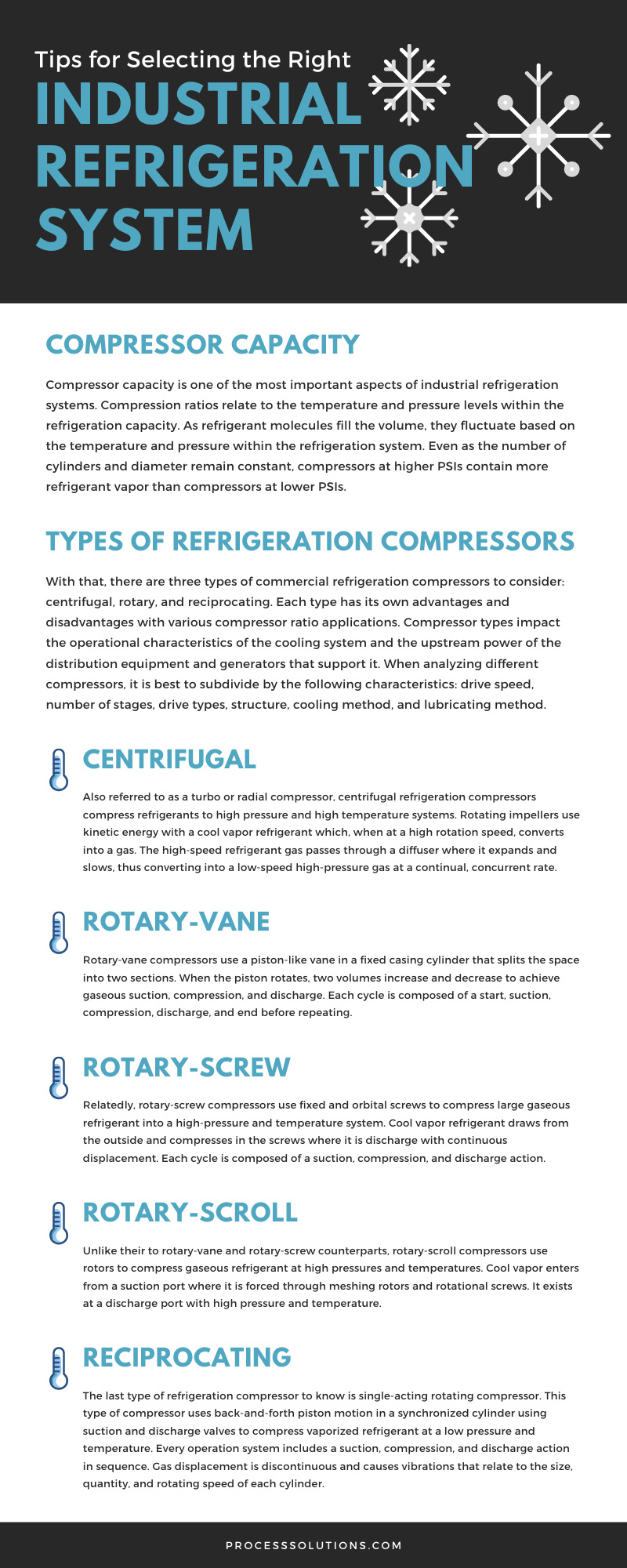