Process Solutions recently built control panels for a food processing customer who specializes in the production of potato products. Along the way, we captured our manufacturing techniques and equipment in order to demonstrate our production abilities and expertise. Follow along and see what gives us the edge in efficiency and helps us produce a consistently high-quality product.
The journey begins in our engineering department, where the bill of materials and electrical design are generated. Once a bill of materials is created and all part tags are assigned, the parameters are sent to our CAD department and development of the back-panel layout begins.
From the CAD Department, the drawings travel to the production floor and are uploaded into our fully automated CNC vertical panel mill. A blank back-panel is then placed on the CNC, and with the touch of a button, drilling begins. This machine drills, taps, and mills every hole in the majority of our enclosures and back-panels.
At the same time as the back-panel is being drilled, a shop technician can begin cutting the wire way and din rail for parts mounting.
With the drilling complete and all wire way and din rail cut, we can begin assembling parts on to the back-panel.
Once all components are assembled on to the back-panel, our technicians begin the wiring process. It is also during this step that the back panel is installed in to an enclosure and wired to any components on the enclosure door.
With the back-panel installed and all wiring complete, the control panel build is now finished. Before we ship a panel, it must go through our testing and quality control phase to ensure the panel is functioning properly and meets our high-quality standards. If everything checks out, the panel is placed into a custom built, fully enclosed wood crate, or loaded carefully into one of our local delivery trucks and shipped to the customer.
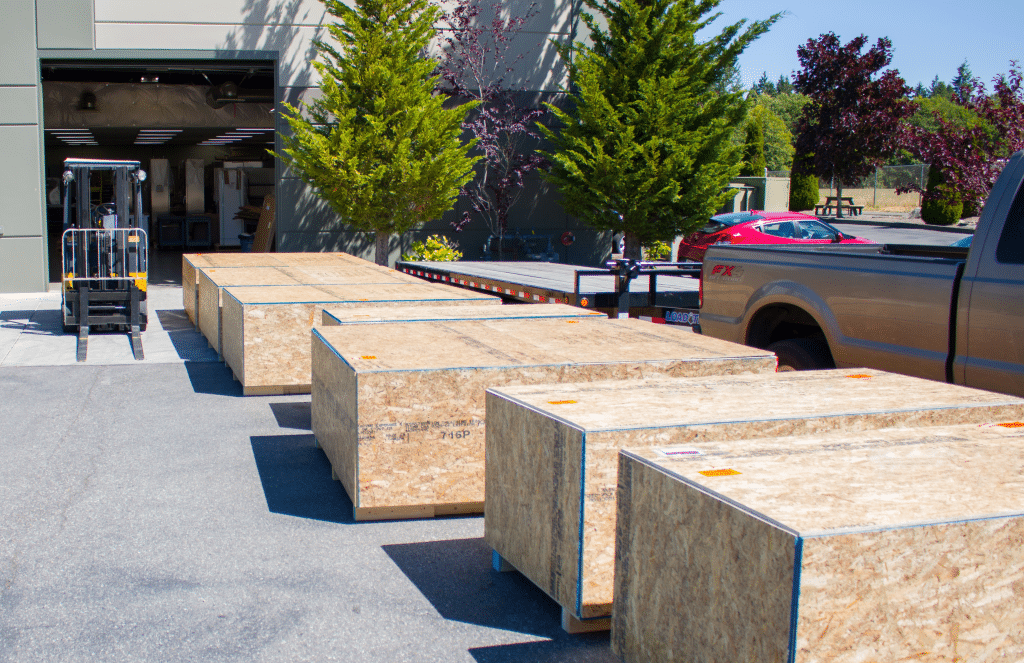