A properly designed and implemented control panel can help boost the performance of your production processes and reduce costs by automating certain tasks. However, when a control panel is improperly designed or poorly maintained, manufacturers may be faced with unnecessary downtime, disruptions, and expensive repairs. By following the simple tips and tricks outlined in this guide, you can ensure you will get the most out of your new or existing industrial control panels.
Proper Documentation
Documentation is an important component of any control system that is often neglected in favor of time and cost savings with unforeseen consequences. The importance of documentation is often not realized until repairs or modifications need to be made to the panel or programs.
By taking the time to create detailed documentation, including functional specifications, electrical schematics, program copies, and panel drawings, you can ensure that you will always have the necessary information to troubleshoot problems, perform required maintenance, or make modifications. Additionally, it’s a good practice to add records of any changes made to your panels, such as scheduled service or system modifications to your documentation.
Indication and Interior Lighting
Adding different types of lights to your control panel can also provide a range of benefits. Exterior indication lights mounted to the panel door, or a stack can provide a quick and clear way to provide information to operators at a glance. For example, indication lights can be implemented that denote system faults, when a process starts or stops, battery life, or whether a device is on or off.
Installing interior enclosure lights is a simple upgrade that can provide a significant benefit to operators or maintenance personnel that need to work inside the panel. Industrial control panels are often installed in dimly lit environments or down narrow hallways. Having interior lights can help those working inside the panel see components and wires more easily, reducing the chance for making mistakes and creating safer working conditions.
Cooling and Internal Temperature Reduction
Heat is one of the greatest enemies of electrical components and control systems. Ensuring your panel can properly disperse heat is vital to keeping your systems running and preventing component failures.
There are several methods for preventing your panel from overheating. These include installing a temperature monitoring device or implementing a machine monitoring application that can alert you before temperatures rise to dangerous levels. Additionally, installing an air conditioning unit with extra capacity for the enclosure size can help maintain a consistent temperature in your panel and prevent overheating.
In scenarios where an air conditioning unit is not required, adding interior fans or enclosure ventilation can also be effective at keeping your panel and components cool. In each of these scenarios, it’s important to remember to regularly clean out dust and debris from your panels, as a dirty air filter or clogged vent can be enough to overheat your system.
Proper Enclosure Type and Sizing
When selecting an enclosure for your control panel, it is important to carefully measure out how much space you will need to fit all your necessary components with enough space for airflow and closing the door. Consider also leaving extra room in the panel for future expansion and additions.
Equally important to proper sizing is selecting the right type of enclosure for the environment in which the panel will be installed. Enclosures come in a variety of materials and designs to suit specific applications. For example, stainless-steel should be used for applications where the enclosure may come into contact with corrosive substances, while mild steel can be used in wet, non-corrosive environments. Referring to a NEMA rating guide can be helpful to determine which enclosure type will be best suited to your specific use-case.
Wiring Layout and Device Labeling
Wiring components in a well thought out and organized manner will result in a cleaner looking panel that will be significantly easier to work on and maintain. To prevent a mess of tangled and hanging wires, utilize wire duct and covers in your panel, always run wires vertically or horizontally instead of diagonally, and layout your panel in an orientation that promotes shorter wire runs.
In addition to organized wiring techniques, implementing a consistent and logical labeling methodology for wires and components can further improve the ability to work on and maintain your panels. For example, engineers can more effectively manage troubleshooting issues or making modifications if they can quickly and easily identify wires and components. When it comes to adhering labels, choose a clearly visible location, such as on the face of the component or each end of a run for wires.
Preventative Maintenance
As with any piece of industrial equipment, being proactive with maintenance can prolong the useful life of your panel and reduce the risk of failure, downtime, and hazardous situations. A regular maintenance schedule should be developed and carried out by a qualified engineer or technician. During scheduled maintenance, be sure to carefully inspect your panel for faulty or frayed wiring, loose connections, worn components, and excessive dust and debris. It is also important to check that all electrical components remain properly grounded.
Once you have finished inspecting your panel, make all the necessary adjustments. Repair or replace worn components and wires, tighten loose connections, and clean out debris using a vacuum or compressed air at proper pressure setting.
About Process Solutions
Located near Seattle, Washington, Process Solutions has over 30 years of experience providing high quality and reliable control systems. With over 100 engineers and technicians on staff and an output of over 3,000 industrial control panels per year, Process Solutions is the Northwest largest control systems integrator. In addition to custom control panel design, build and commissioning, Process Solutions’ control systems services include PLC and HMI programming, robot system integration, energy management and refrigeration systems, SCADA software, and DAQuery machine monitoring software.
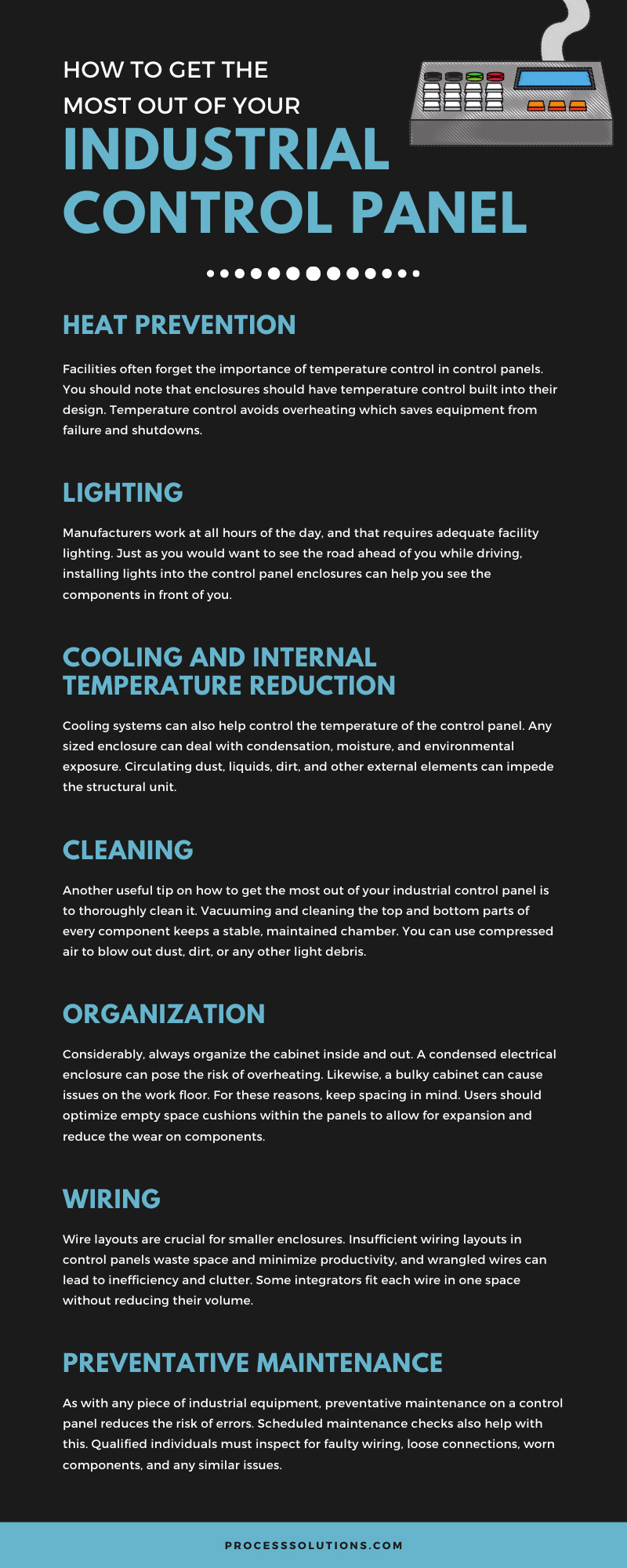