Control panels contain electrical components and devices that allow for the automation of industrial processes and equipment. When designing a custom control panel, there are a number of key aspects to consider to ensure your panel operates properly, is safe to use, and remains reliable. Understanding the basics of what to consider in industrial control panel design will help ensure your panel meets your specific requirements and reduces the chances for costly mistakes during your project.
PANEL LAYOUT AND DESIGN
Designing an industrial control panel requires careful consideration of every aspect of your manufacturing process, equipment, and plant environment. This knowledge is necessary when determining what type of enclosure is needed, the available space to install the control panel, what the electrical requirements are, and what hardware and software components are needed to achieve your desired functionality. While a custom control panel is designed to suit a specific application, most share a similar overall blueprint.
Enclosure Type and Sizing
Determining the enclosure type and size for your control panel is an important step in the design process. When choosing the enclosure type, we evaluate the environment that the panel will be located in. For example, a panel that will be exposed to corrosive substances will need a fully sealed stainless-steel enclosure, while a panel that is installed in an area with high ambient temperature may require a ventilation fan or air conditioner. Furthermore, a panel that is being mounted to a machine, pedestal, or on a wall will use a different style enclosure than a panel that will be free-standing.
Once the enclosure type has been selected, we determine the right size based on the space required to install and wire the intended control panel components. Additionally, the National Electric Code (NEC) includes requirements for proper wiring space and wire bending radius.
Power and Circuit Protection
Assessing your power requirements is another important step when designing a custom control panel and is best handled by a qualified controls engineer. Conducting full-load calculations will help you determine how many amps will need to be supplied to the panel. Furthermore, based on the voltage of the power supplied by your facility, you may need to include a transformer in your panel to convert the voltage to 120V AC and/or a power supply to convert to 24V DC.
The types of equipment you will be controlling also must be considered when assessing your panel’s electrical requirements. For example, if your panel will be controlling motors, you may need to include contactors, overload relays, or motor starters to protect your motor from pulling too much electrical current and overheating.
Determining correct wire sizes to ensure delivery of the required load current, as well as adding the necessary circuit protection are additional aspects that are crucial to the electrical design of your panel. Circuit protection is essential for creating consistency and preventing damage to your wires and components from excessive voltages or currents. Circuit protection components may include circuit breakers, surge protectors, and fuses.
Controls Components
Selecting the right components and devices to accomplish the control functionality you need is another step of designing a custom control panel. Control components such as relays or timers may be used in simple control applications where you just need the ability to turn something on or off based on an input signal.
More complex applications such as those requiring the ability to control a sequence of events may require a programmable logic controller (PLC), which is a microprocessor specially designed to operate in harsh industrial environments.
If you are controlling a motor, depending on the application, you may need a variable frequency drive (VFD), servo drive, or soft starter in your panel. A VFD is used in situations where you need to control motor speed. Alternatively, servo drives are used with servo motors and can control multi-axis movements. Finally, soft starters are used to gradually increase the voltage supplied to a motor during start-up to prevent a high rush of current and torque that can damage the motor and the equipment being driven.
Operator Interfaces
The control panel’s operator interface can take many different forms, including pushbuttons, switches, indicator lights, digital meters, or human-machine interface (HMI) display. Each of these interfaces can be used on their own or in conjunction with one another, depending on the level of functionality you need. The advantage of using an HMI in your design is the ability to combine all your pushbuttons, switches, and meters into one digital touch screen display. Additionally, when integrated with SCADA software, HMIs also provide an overview and control of your facility and ongoing processes, as well as alarm indicators, visualization of machine metrics, and production reports.
Safety and Regulations
Process Solutions, as well as any other control panel builder, must comply with certain control panel and electrical regulations to ensure safety. The main industrial control panel codes and standards include:
- UL 508A – Standard for Industrial Control Panels intended for general use.
- UL 698A – “Standard for Industrial Control Panels Relating to Hazardous (Classified) Locations.”
- NFPA 70 – “Standard for safe installation of electrical wiring and equipment.”
- NFPA 79 – “Electrical Standard for Industrial Machinery to protect operators, equipment, facilities, and work-in-progress from fire and electrical hazards.”
Safety is a top concern when designing a control panel. Implementing a disconnect switch to completely shut off power before performing maintenance or during an emergency is just one way to promote safety. Furthermore, using the lowest practical voltages, touch-safe components, and following NEC and UL regulations also helps make the control panel safer to use.
Control Panel Maintenance
Once your custom control panel has been designed, built, and installed, it is important to perform continued maintenance to ensure safety and reliability. Simple maintenance practices that can be performed to prolong the life of your control panel include:
- Keeping pests away from panel wiring and out of the enclosure.
- Regularly clearing out dust build-up. Be careful not to vacuum near circuit boards without following electrostatic discharge (ESD) rules.
- Periodically checking terminal connections to ensure they remain properly tightened.
- Always keep the enclosure door closed.
- Contacting your systems integrator to perform any necessary software updates.
About Process Solutions
Located near Seattle Washington, Process Solutions is the Northwest’s largest control systems integrator. With 30+ years in business and over 100 engineers and technicians on staff, Process Solutions has the experience and capacity to take on almost any automation project. Process Solutions provides a wide range of control system services, including electrical control panels, PLC and HMI programming, robot system integration, energy management and refrigeration systems, SCADA software, and machine monitoring software.
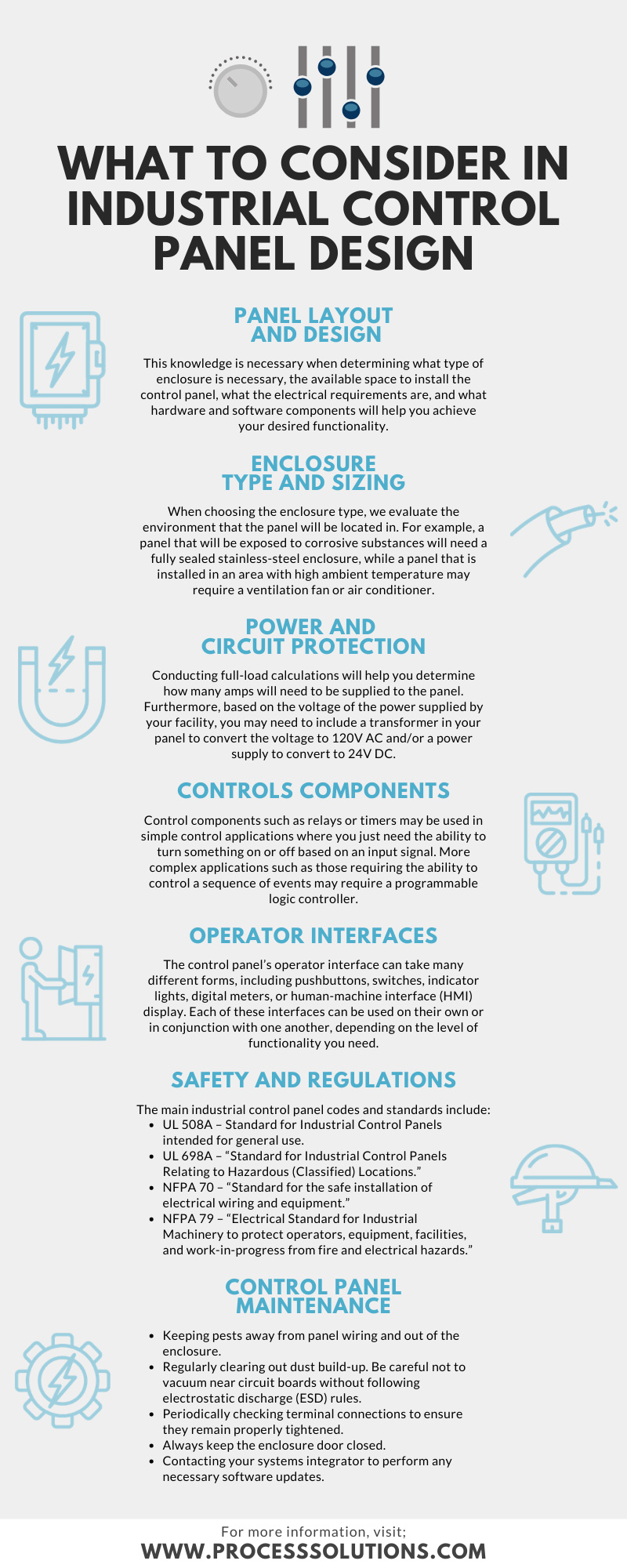